Demand Flow Technology (DFT) improves business processes by focusing on customer demand. It uses mathematical tools to connect processes to daily demand changes. DFT applies a scientific approach to flow manufacturing, especially in discrete production. It centers on demand pull, guiding activities based on real-time customer needs. This differs from schedule-push systems that rely heavily on forecasts.
DFT effectively tackles inefficiencies in traditional manufacturing systems. It enhances production flow by aligning with actual demand patterns. This approach significantly reduces waste, saving resources and time. DFT also improves product quality, efficiently meeting customer expectations. By focusing on demand, DFT ensures precision and accuracy in manufacturing.
This article aims to provide a detailed understanding of DFT. It highlights its benefits for modern supply chains and manufacturing and focuses on how DFT transforms business processes through demand-driven strategies. Readers will gain insights into DFT’s applications and impact on production.
In this blog post we will learn in detail about What is Demand Flow Technology?
Importance of Demand Flow Technology
The Concept of Demand Flow
Demand Flow Technology (DFT) prioritizes aligning production with actual customer demand. It shifts from traditional push systems to demand-driven pull systems. DFT utilizes real-time data to adjust manufacturing processes effectively. This approach ensures that production meets customer needs accurately. By aligning processes with demand, waste and inefficiencies decrease.
History and Origins of Demand Flow Technology
Demand Flow Technology traces its roots back to the 1990s. John R. Costanza created the methodology during his time in prominent companies. He founded the Demand Flow Technology Institute to promote education and consultation. Influences include Lean Manufacturing, Just-in-Time (JIT), and Theory of Constraints (TOC).
Early adopters recognized its potential for efficient production management. DFT incorporated techniques like Kanban from the Toyota Production System. The methodology evolved into a lean manufacturing approach for handling diverse production needs.
Also Read: What is WPB technology?
What are the Core Principles of Demand Flow Technology?
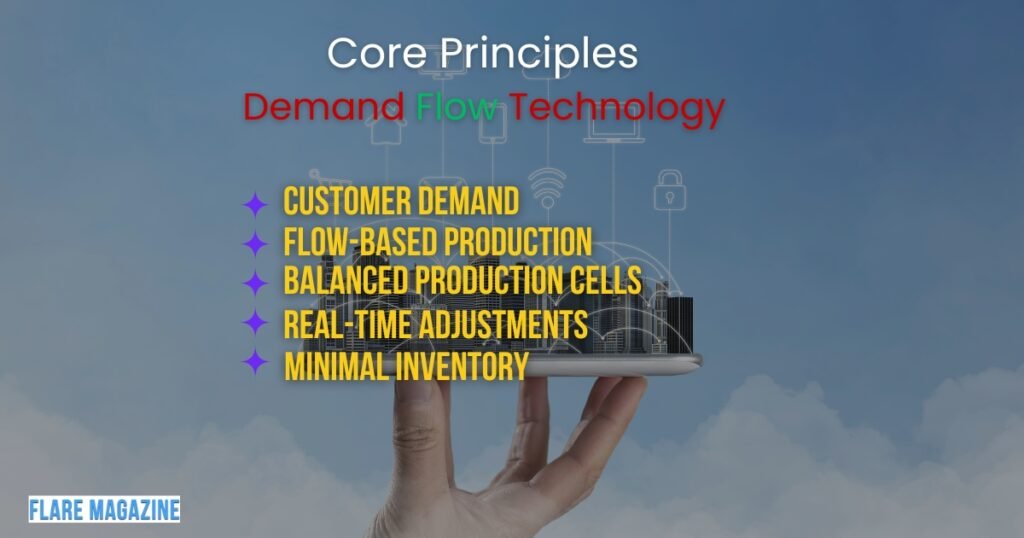
Customer Demand as the Driving Force:
The central principle of DFT bases production on actual customer demand, not forecasts. This approach ensures operations respond promptly to real-time market needs.
According to Aberdeen Group, demand-driven manufacturing creates a synchronized loop between orders and execution.
Flow-Based Production:
DFT targets continuous flow in material and product movement, thus reducing bottlenecks. This continuous flow approach aids in maintaining efficiency across operations. By coordinating material flow, DFT effectively aligns production with demand.
Balanced Production Cells:
In DFT, production cells operate in balance, minimizing idle times and waiting. These cells are designed to match production rates with demand rates continuously. This balance ensures optimal utilization of resources.
Real-Time Adjustments and Flexibility:
DFT allows for real-time changes in production schedules as demand shifts. This flexibility is crucial for modern manufacturing to adapt quickly. Real-time adjustments enhance responsiveness to market and customer changes.
Minimal Inventory:
DFT reduces or eliminates excess inventory, focusing on producing only what’s needed. Production aligns closely with actual orders, minimizing stock levels. This practice releases cash from working capital for growth and innovation.
How Demand Flow Technology Works?
Production Process:
The production system responds directly to customer demand signals with precise adjustments. Customer orders integrate with production schedules and efficiently guide inventory management strategies.
This seamless integration ensures that production only occurs when actual demand is present. Production lines adjust based on real-time data to meet immediate customer needs. Reducing waste and unnecessary production enhances the efficiency of manufacturing processes.
Role of Technology and Software:
Advanced software systems support DFT by accurately tracking demand and production status. These systems deliver up-to-date information on supply chain activities to stakeholders. Companies utilize software tools for real-time demand tracking and production adjustments.
The advanced technology allows accurate forecasting and enhances collaboration in manufacturing. Demand Flow uses software systems to maintain production efficiency and responsiveness.
Flow Control and Pull Mechanism:
The pull system signals upstream production processes to start manufacturing efficiently. Downstream processes alert upstream activities when additional production is required. This approach ensures no excess production, maintaining lean operations in real time.
Pull mechanisms enhance coordination between various production stages and improve flow. This integration prevents bottlenecks and significantly reduces material and product idle times.
Modular and Flexible Design:
Production systems using DFT are modular, allowing easy adaptation to changing demands. Companies can reconfigure production setups quickly to align with market shifts effectively. The modular approach aids in scaling processes with minimal disruption in production.
Flexible designs support rapid changes in production volumes and product types. Adapting quickly to demand changes minimizes downtime and boosts efficiency.
Benefits of Demand Flow Technology
- Increased Efficiency: DFT optimizes resources by cutting unnecessary steps, improving overall workflow efficiency. This process ensures resources are targeted where they are truly needed most.
- Reduced Lead Times: DFT reduces lead times by aligning production closely with actual customer demand. Real-time adjustments seamlessly synchronise production activities with incoming orders.
- Cost Reduction: DFT lowers operational costs by minimising inventory and significantly reducing production waste. Streamlined processes enhance cost-effectiveness in manufacturing operations.
- Improved Quality and Consistency: DFT ensures consistent product quality through standardized processes across manufacturing activities. It promotes uniformity in production techniques for reliability.
- Enhanced Customer Satisfaction: Aligning production with demand helps deliver products swiftly and accurately to customers. Timely deliveries improve satisfaction, fostering stronger relationships with clients.
Challenges in Implementing Demand Flow Technology
Initial Investment: Implementing DFT involves significant capital costs for new equipment and software. Companies must invest in employee training to ensure successful DFT practices.
The initial investment may appear daunting but promises long-term efficiency gains. Business leaders often weigh upfront costs against future operational savings.
Resistance to Change: Employees may resist transitioning from familiar systems to DFT approaches. Managers prefer traditional methods that they know well over new systems.
Encouraging staff to adapt to DFT requires strategic change management. Communication and training can help overcome resistance and facilitate smoother adoption.
Complexity in Customization: DFT systems need customization to fit a company’s specific needs effectively. The customization process can become complex for unique industry requirements.
Businesses should ensure tailored solutions for maximum benefits from DFT. Customization aligns DFT processes with individual goals and operational demands.
Supply Chain Dependencies: DFT relies heavily on the alignment of the entire supply chain. Suppliers and distributors must adjust to demand-based production for DFT success.
Effective communication between supply chain partners is crucial for seamless operations. A synchronized supply chain enhances the benefits of implementing DFT.
Applications of Demand Flow Technology
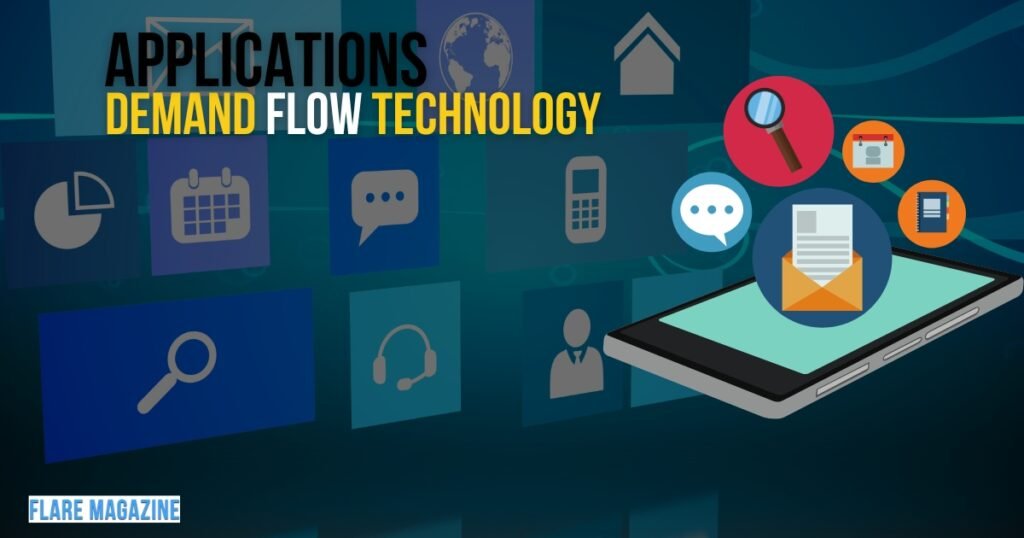
Manufacturing Industries
Automotive: Automotive manufacturers use DFT to align production with current vehicle demand accurately. Demand Flow enhances efficiency by reducing waste and optimizing resources in vehicle manufacturing.
Manufacturers achieve shorter lead times and maintain lower inventory levels through DFT. Real-time data assists automotive companies in adjusting production schedules as demand varies.
Electronics: Electronics makers employ DFT to synchronize production with real-time consumer electronics demand. DFT effectively reduces inventory costs by aligning production closely with actual demand.
Manufacturers can adapt quickly to technological trends using demand-driven flow technology. Systems ensure efficient production using precise tracking of customer purchase patterns.
Consumer Goods: Consumer goods industries benefit from DFT by optimizing production according to changing customer needs. Demand Flow minimizes overproduction by tailoring outputs to real-time demand analytics.
This strategy helps companies remain agile in rapidly shifting consumer markets. DFT supports sustainable practices by reducing waste and focusing on necessary production.
Healthcare: Healthcare facilities use DFT to manage medical supplies and ensure efficient equipment production. The technology aligns supply chains with current hospital and patient equipment demand proficiently.
Medical facilities reduce waste and enhance resource allocation using demand-synchronized processes. DFT application ensures consistent availability of essential healthcare resources and equipment.
Food and Beverage Industry: Food producers adapt DFT to align food production with fluctuating customer demand precisely. Demand Flow minimizes waste by synchronizing outputs with actual market trends effectively.
This adaptability supports sustainable practices by minimizing excess production and conserving resources. The industry enjoys smoother operations through demand-driven flow management techniques.
E-commerce and Retail: E-commerce companies implement DFT to synchronize product availability directly with customer demand trends. Businesses optimize inventory management by aligning offerings with real-time shopping behavior data.
DFT supports prompt adjustments in order processing and restocking strategies efficiently. Retailers maintain streamlined operations by balancing supply with consumer demand fluctuations.
Case Studies of Demand Flow Technology in Action
Toyota
Toyota implemented Demand Flow Technology to streamline its automotive production processes effectively. They reduced production costs and improved overall efficiency through synchronized production. By aligning manufacturing with real-time demand, Toyota minimized waste and inventory expenses.
Customer satisfaction increased with timely deliveries and high-quality vehicles consistently produced. This approach led to significant cost savings and stronger customer relationships globally.
Samsung
Samsung faced challenges while integrating Demand Flow Technology in its electronics manufacturing units. Adjusting existing systems required significant investment and detailed staff training initiatives.
Despite initial resistance, Samsung achieved faster production cycles and reduced inventory levels. They adapted to technological market changes swiftly, enhancing product availability in diverse regions. Improved communication among supply chain partners led to smoother operations globally.
Lessons Learned
Successful DFT implementation requires investment in technology and extensive employee training programs. Customize systems to meet specific requirements, ensuring alignment with company goals efficiently.
Overcoming resistance to change involves strategic management and clear communication with staff. Real-time data usage enhances production accuracy and minimizes unnecessary inventory effectively. Maintaining strong supply chain relationships ensures ongoing synchronization and seamless operations.
Future of Demand Flow Technology
Advancements in Technology
Artificial intelligence (AI) transforms demand forecasting using precise decision-making algorithms. Machine learning interprets data patterns, predicting demand trends accurately for improved DFT outcomes.
Internet of Things (IoT) devices enable real-time monitoring, offering insights into production and supply changes. These technologies enhance DFT precision by connecting data sources seamlessly for strategic operations.
Integration with Industry 4.0
DFT integrates with Industry 4.0 for automated, data-driven manufacturing systems with flexible operations. Smart factories use advanced sensors and robotics to align production with current demand.
Data analytics tools provide instant feedback, improving manufacturing efficiency and resource use effectively. Industry 4.0 technologies allow companies to adapt production workflows promptly to market changes.
Sustainability and Green Manufacturing
DFT supports sustainability by reducing waste through aligning output with real-time demand forecasting. It minimizes energy consumption by planning production cycles more efficiently in manufacturing processes.
Green manufacturing emissions declined as DFT helped optimize both production and logistics. Adopting DFT leads to sustainable operations, enhancing environmental responsibility in various industries.
FAQ’s
What is the Demand Flow Process?
The Demand Flow Process aligns production with actual customer demand. It reduces waste by synchronizing outputs to market needs, improving efficiency and resource use, and ensuring that manufacturing processes remain responsive to real-time demand trends efficiently.
What is DFT Technology?
DFT Technology uses real-time data to optimize production. It minimizes inventory by syncing supply with demand, enhancing operational efficiency through technological integration, and provides actionable insights into supply chain performance to adapt to changing market requirements promptly.
How does Demand Flow Strategy help supply chains?
Demand Flow Strategy balances supply with real-time demand. It ensures efficient resource utilization, reduces unnecessary stock levels, minimizes production delays, and supports quick response to market shifts, thereby bolstering the overall supply chain flexibility and resilience.
Why is Demand Flow important in manufacturing?
Demand Flow reduces unnecessary production and waste. It aligns manufacturing with current demand trends, lowering costs while improving delivery times, ensuring manufacturers maintain high levels of customer satisfaction with better product availability and quality across target markets.
Can small businesses use DFT Technology?
Yes, small businesses benefit from DFT Technology. It tailors processes to demand trends, enhancing market responsiveness and reducing costs, allowing even small companies to enjoy streamlined operations and improve their overall competitiveness in dynamic industries.
Conclusion
Demand Flow Technology optimizes production by aligning it closely with real-time customer demand. It reduces waste, lowers inventory costs, and improves supply chain efficiency effectively. Industries like healthcare and e-commerce benefit from streamlined operations and enhanced resource management.
Businesses should consider DFT as a tool for improving efficiency in competitive markets. Adopting DFT can help meet modern customer demands swiftly and effectively. DFT supports sustainability by reducing production waste and conserving resources responsibly.
To adopt DFT, assess your current systems for areas needing improvement. Explore pilot projects to test the feasibility of DFT in your business. Invest in employee training to ensure a smooth transition to demand-driven operations.